Originally printed in The Rivendell Reader, Issue 22, Winter 2001
First
we look the frame over for any obvious problems (dents, rust, pin holes,
bulges, alignment, etc.) This gives us the opportunity to check out the
builder's work -and critique the workmanship. We call this "bus driving."
We then put toothpicks in the breathing holes, bolts in the water bottle
bosses and plugs in the bottom bracket and head tube so that sand will
not get inside the tubes during the blasting process.
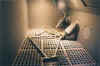
For an illustrated guide to a
JB paint job, click here
|
Next we put the frame into the blasting cabinet and sandblast the frame
clean to insure a good bond between primer and metal. We use a special
pressure-pot cabinet because it is designed to yield superior results
with half the air pressure that would be needed with a siphon feed cabinet.
Normal air pressure is 35-45 psi as opposed to 75-90 psi. This is much
better for the frame and doesn't make the air compressor work as hard.
Our choice of blasting media is 60 grit garnet sand because we like the
fine "tooth" that it etches on the frame to promote paint adhesion. It
is lavender in color. Coarser grits and higher blasting pressures are
the way metal is cleaned for most industrial finishes, but is not appropriate
for relatively thin walled bicycle tubing. Another reason we prefer garnet
as opposed to other media is because when it hits the metal, it tends
to break down rather than keep its original shape. This insures that the
media does not imbed itself in the metal, causing stress that could lead
to a potential failure down the road. A popular blasting media known as
aluminum oxide has been known to do this to lightweight steel. It costs
about the same as garnet ($30.00 / 90 lb. bag) but the garnet is more
desirable because it's more gentle.
After the toothpicks, bolts and plugs are removed and excess dust is blown
off, we bring the frame into the spray booth for the first coats of epoxy
chromate primer. The frame is then force dried in a small room with a
heater at approximately 150 degrees F. for one hour.
Then we look for minor imperfections and touch them up with spot putty (bondo). When the putty
dries, we sand it, smooth it, and apply primer.
When this is dry the whole frame is carefully sanded smooth with 320 grit
dry sandpaper. It is now ready for top coating. The frame is then blown
off with air and sprayed with a special radioactive static eliminator
nozzle to greatly reduce dust nibs caused by small airborne debris. If
the frame is a Rivendell, then the head tube is sprayed with DuPont Imron
Polyurethane enamel #4296 Cream in three coats, with a flash time of 10-15
minutes between each coat. After sitting overnight or one hour in the
oven the head tube is now carefully masked using only the finest quality
3M automotive masking tape. It's expensive tape, but well worth it as
it leaves no adhesive residue and comes off easily when it's time to pull
off. Just try spraying and baking urethane over Home Depot tape and then
removing it and you'll see what I'm talking about. The tape is then delicately
cut with a virgin #11 x-acto blade right in the corner of the tube and
the lug. A special tool is used to make sure the tape is laying down properly.
This process separates the men from the boys in bike painting. The cream
overspray that was not masked is re-scuffed with 320 grit and blown off
once again with air and then the ray gun. We're now ready to mix paint!
After making sure the frame is clean, we make sure the spray booth is
relatively sanitary and then suit up and don the face mask that will supply
clean air that is piped in from a remote pump that is feeding air at the
rate of 15psi. This is necessary because DuPont Imron fumes are toxic.
The can of paint is selected, opened, stirred thoroughly and mixed in
a ratio of 6 parts paint to one part high solids activator and one part
reducer with a smidgen of paint additive thrown in for insurance against
contamination. The activator is the good stuff that makes the paint kick
off. It has lots of wonderful ingredients like aliphatic polyisocyanates,
ester solvents and xylene. Wonderful brew, indeed. They have to make the
container for it extra large just so they can fit the warning label on
it. I get the bro' deal on this stuff and it still costs me 300 bucks
a gallon. But I'm digressing here.
Three topcoats are skillfully applied with a 10-20 minute flash time between
coats, depending on temperature. After sitting overnight, the masking
tape is carefully removed and the transition area between the main color
and the cream is gently scraped with the x-acto blade to remove any excess
tape or paint build-up. Decals are now applied and the first coat of cream
is painted in the cutout windows around the frame. About twenty minutes
in the oven to cure the decal adhesive and make sure cutouts are dry and
we're ready for clear coats. One good solid un-reduced coat over the entire
frame and fork with several coats over the decals and it's off to the
oven for an hour at 150-160 degrees F.
Time for the fun part. By this time, even with all the babysitting the
frame has been through, there's always some dust nibs in the paint. So
we break out the 320 grit dry paper and sand the clear smooth. Don't fall
asleep at the sandpaper and go through the clear to the color because
you've really blanked it up when that happens.
Now we have all these 320 grit scratches in the clear coat. We want to
get as good a gloss as we can, so we're going to make those scratches
a lot finer by wet sanding with 1000 grit sandpaper. I might add here
that we've already gone way beyond where production bike painters have
already finished, cleaned the gun, shipped the frame and are well into
that second 12 pack of Old Milwaukee. Only the best custom painters are
left in the room now.
Okay; now we wipe down the frame and get it really clean with no sanding
backwash left. The second coat of paint is applied in the cutouts. This
is necessary so that you can't see through the cutout and see the color
of 'the frame underneath. It really does count; just look at some of the
Italian imports (the ones that still have lugs and cutouts). It looks
like they paint the windows with a worn out toothbrush. The lug line of
the head tube is gone over with the cream as well as the pinstripe around
the top and bottom head lugs. A little more close inspection and fussing
over the frame and we're ready to go back into the booth for the final
time. More wiping down, blowing air, ray gun action, a little prayer to
the paint god and we lay down three coats of clear Imron, baby! A little
more reducer in each successive coat for increased flowout and we are
now running the ragged edge between liquid glass and run city. Let it
sit for awhile to flash off and try not to trip while carrying it in to
the baking room.
I usually like to let it sit overnight and cure slowly before giving it
an hour of oven time the next day. Now it's time to look it over and see
if any errant dragonflies have landed on the top tube and stumbled along
in a fog leaving their tracks in a crooked path before being overcome
by cyanate fumes and becoming permanently encased in the ever hardening
clear coat.
If all looks good, the tape is pulled off the shift bosses and
from inside the head tube and a clear vinyl chain-slap protector is laid
down on the right chain stay so that it disappears�a little extra protection
where it's needed. We also write the date it was finished on the steering
column for future reference. All my records of paint jobs are categorized
by date of completion.
Well, there you have it. It's not easy or fast, but it's nice to do something
for a living that people like to look at, can appreciate for many years,
makes them want to ride their bike, and with a little luck will lead to
many happy memories.
|